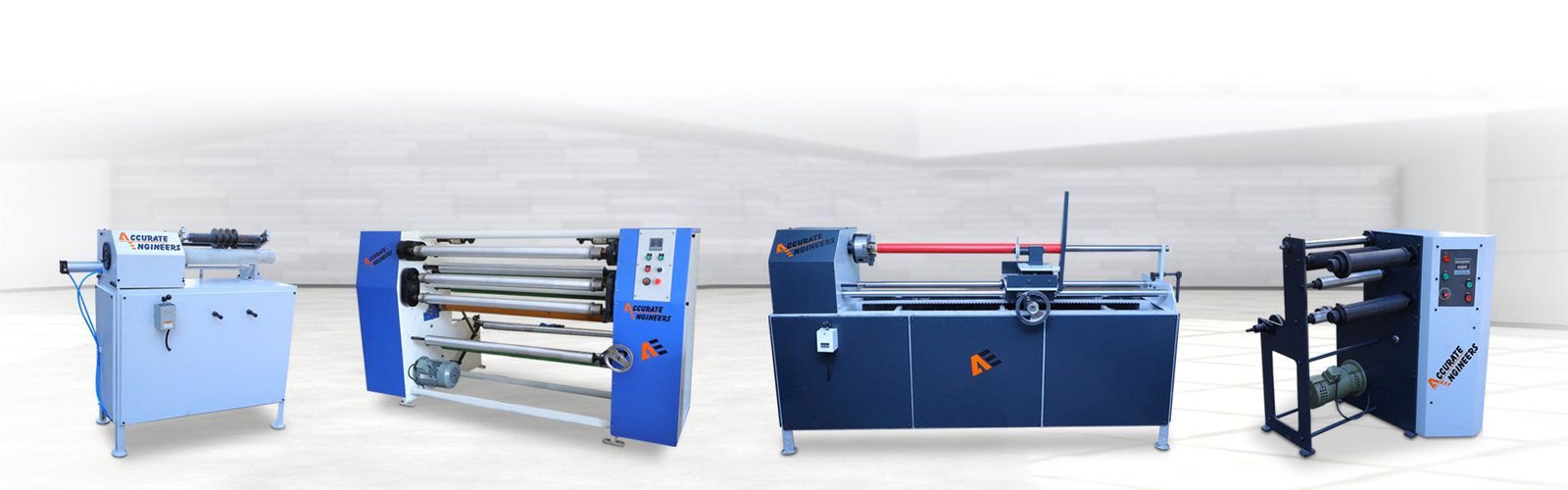
Enhancing Productivity: The Versatility of Cello Tape Slitting Rewinding Machines
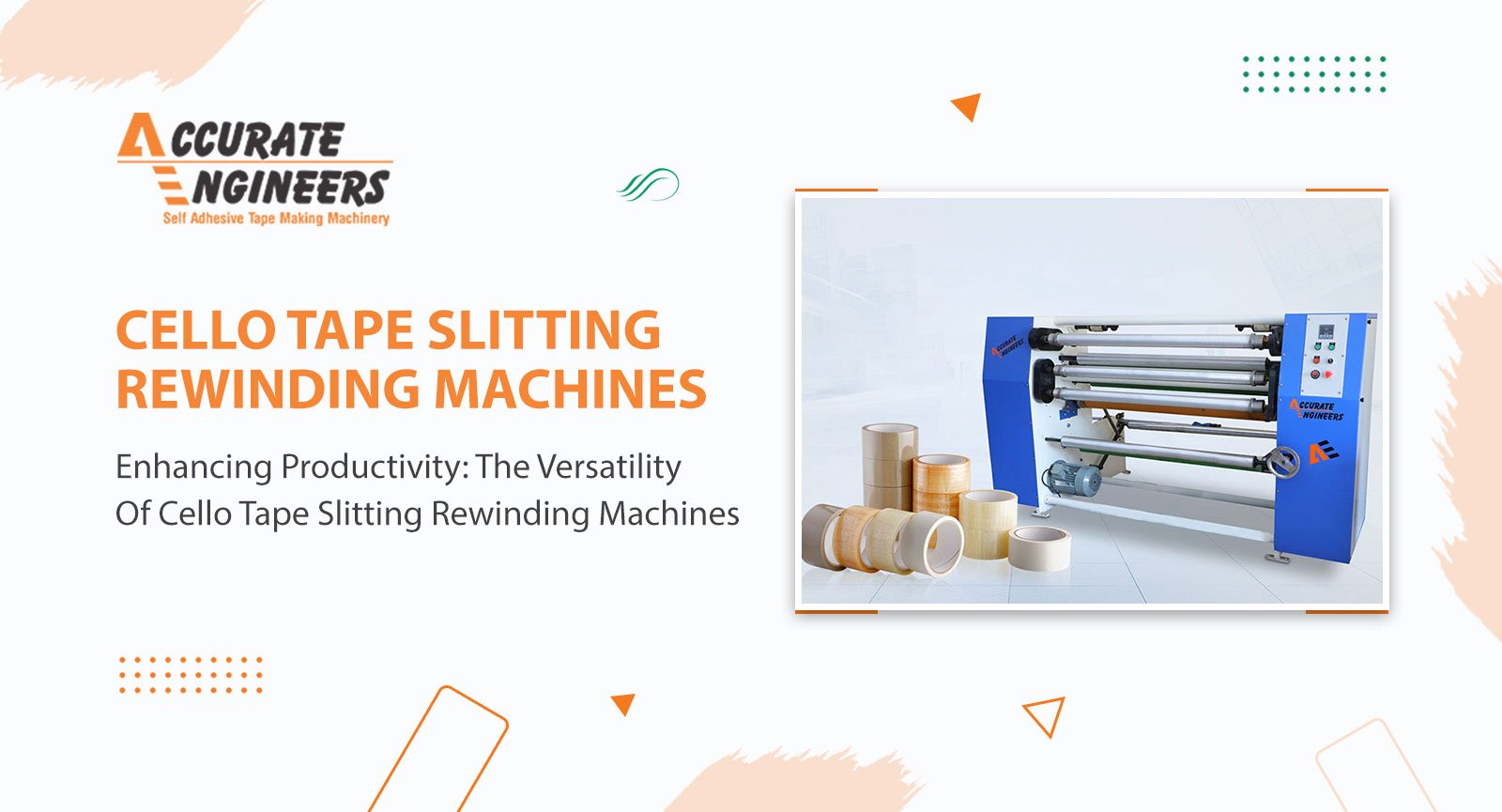
Cello Tape Slitting Rewinding Machines By Accurate Engineers Leave a comment
The Fundamentals of Cello Tape Slitting and Rewinding
Slitting and rewinding machines for cello tape are an essential component in the process of reducing the size of huge rolls of tape to smaller, more manageable rolls. These machines are made up of a variety of parts, such as a control panel, unwind unit, rewind unit, slitting system, and tension control mechanisms. Unwinding the tape, precisely slitting it, rewinding it onto smaller cores, and keeping the tension consistent throughout the operation are the steps that make up the process.
Working Principles of Cello Tape Slitting and Rewinding Machines
Components such as slitting knives, rewinding shafts, and web guidance systems guarantee that the web is aligned correctly, that tension is controlled, and that the edge is trimmed. When it comes to producing high-quality work, the synchronisation of these components as well as the precise management of the pace and tension play an extremely important role.
- Flexibility
Flexibility is one of the most significant benefits offered by Cello Tape Slitting Rewinding Machines, and it is also one of the machines’ primary selling points. These machines are able to accommodate a broad variety of tape types, including speciality tapes, double-sided tapes, masking tapes and packing tapes, among others.
The fact that the machines are able to work with a variety of widths, thicknesses, and adhesive formulas gives producers the flexibility they need to make tapes that are customised to meet the needs of individual customers. Additionally, modifications like printed tapes or perforations may be readily integrated, which expands the variety of applications that can be used with the product.
- Efficiency
These machines are created by Cello Tape Slitting Rewinding Machine Manufacturers in India with the intention of increasing both the efficiency and productivity of the tape production process. These machines provide producers the ability to increase their manufacturing output by a significant amount because of their high-speed operating capabilities, automated tension control mechanisms, web guiding systems, and modern control panels with programmable settings.
The components are kept under exact control, and they are synchronised with one another, which results in accurate slitting, constant tension, and low material waste. Monitoring systems and sensors that operate in real time provide input on the quality of production and make it possible to quickly diagnose and fix problems.
- Control and inspection of quality
Ensuring the consistent high quality of the tape throughout the production process is of the utmost importance. Slitting and rewinding machines for cello tape often include quality control and inspection devices to guarantee that the finished product is of a high standard. In-line inspection technologies are used in order to identify flaws, monitor the application of glue, and guarantee that the breadth and thickness remain constant.
It is vital to undertake routine maintenance and calibration on Electrical Tape Making Machine in order to maintain optimum performance and provide tapes that live up to the standards set by the customers.
- Operational Safety and Maintenance
Running cello tape slitting and rewinding machines in a safe manner and performing routine maintenance is two of the most important factors in determining long-term production and the well-being of the operators. Important factors that should be considered for worker protection include correct machine guarding, emergency stop systems, and operator training.
Maintenance tasks like as cleaning, lubrication, and blade sharpening should be performed on a regular basis to guarantee a smooth functioning and reduce unplanned downtime. It is very necessary, in order to maintain a safe and productive working environment, to adhere to the procedures and recommendations set out by the manufacturer.
Conclusion
The production of cello tape has been revolutionized by machines that slice and rewind the tape, which has resulted in increased output of higher quality and increased productivity. Because of the adaptability of these machines, producers are able to satisfy the expectations of their customers in a timely manner and cater to a broad variety of tape kinds. Tape producers can maximize their production and maintain their competitive edge in the market by focusing on areas such as improving operational safety and maintenance, controlling the quality of their products, and assuring quality assurance.
Among the many products that Accurate Engineers Supplier in India makes are printing machines, rewinding machines, and slitter-rewinding machines, among others.